The Working Principle And Difference Of Brushed Motor And Brushless Motor In Electric Screwdriver
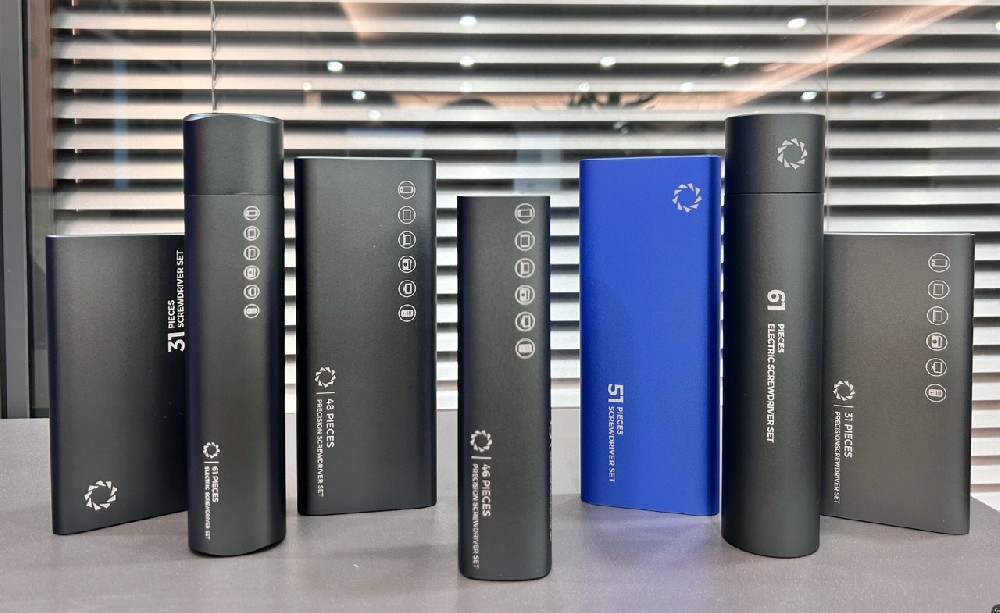
Working Principle of Brushed DC Motor
The main structure of a brushed DC motor is stator + rotor + brush, which obtains torque through a rotating magnetic field and outputs kinetic energy. The brush is in constant contact and friction with the commutator, which plays a role in conducting electricity and commutating phases during rotation.
Brushed DC motors use mechanical commutation, the magnetic poles do not move, and the coils rotate. When the motor is working, the coils and commutator rotate, the magnets and carbon brushes do not rotate, and the alternating change of the coil current direction is completed by the commutator and brushes that rotate with the motor.
In a brushed DC motor, the process is to arrange the two power input terminals of each group of coils in a ring in sequence, separated by insulating materials, to form a cylinder-like thing, which is connected to the motor shaft as a whole. The power is passed through two small pillars made of carbon elements (carbon brushes). Under the action of spring pressure, it presses on two points on the upper coil power input ring cylinder from two specific fixed positions to energize a group of coils.
As the motor rotates, different coils or different poles of the same coil are energized at different times, so that the NS pole of the coil generating the magnetic field has a suitable angle difference with the NS pole of the permanent magnet stator closest to it. Opposite poles of the magnetic field attract each other and like poles repel each other, generating force to drive the motor to rotate. The carbon electrode slides on the coil terminal, like a brush brushing on the surface of an object, so it is called a carbon "brush".
When sliding against each other, the carbon brushes will rub against each other and cause wear, which requires regular replacement of the carbon brushes. When the carbon brushes and the coil terminals are switched on and off alternately, electric sparks will occur, generating electromagnetic damage and interfering with electronic equipment.
Working Principle of Brushless DC Motor
In a brushless DC motor, the commutation work is done by the control circuit in the controller (usually a Hall sensor + controller, a more advanced technology is a magnetic encoder).
Brushless DC motors use electronic commutation, the coil does not move, and the magnetic poles rotate. Brushless DC motors use a set of electronic devices to sense the position of the permanent magnet poles through the Hall switch SS2712 . Based on this perception, electronic circuits are used to switch the direction of the current in the coil in a timely manner to ensure that the magnetic force in the correct direction is generated to drive the motor. The shortcomings of brushed DC motors are eliminated.
These circuits are motor controllers. The controller of the brushless DC motor can also realize some functions that the brushed DC motor cannot realize, such as adjusting the power switching angle, braking the motor, reversing the motor, locking the motor, and using the brake signal to stop the power supply to the motor. The electronic alarm lock of the current battery car makes full use of these functions.
The brushless DC motor consists of a motor body and a driver, and is a typical mechatronics product. Since the brushless DC motor is operated in an automatic manner, it does not require an additional starting winding on the rotor like a synchronous motor that starts under heavy load under variable frequency speed regulation, nor does it produce oscillation and loss of step when the load changes suddenly.
The difference between brushed DC motor and brushless DC motor speed regulation
In fact, the control of both motors is voltage regulation, but because the brushless DC uses electronic commutation, it requires digital control to be realized, while the brushed DC is commutated by carbon brushes and can be controlled using traditional analog circuits such as thyristors, which is relatively simple.
1. The speed regulation process of brushed motor is to adjust the voltage of the motor power supply. The adjusted voltage and current are converted through the commutator and brushes to change the strength of the magnetic field generated by the electrode to achieve the purpose of changing the speed. This process is called variable voltage speed regulation.
2. The speed regulation process of brushless motor is to change the speed by changing the control signal of the electric regulator while keeping the voltage of the motor power supply unchanged, and then changing the switching rate of the high-power MOS tube through the microprocessor. This process is called variable frequency speed regulation.
Performance Differences
1. Brushed motors have a simple structure, a long development time, and mature technology.
As early as the 19th century when the motor was born, the practical motor produced was a brushless type, that is, the AC squirrel cage asynchronous motor, which was widely used after the generation of alternating current.
However, asynchronous motors have many insurmountable defects, which has led to slow development of motor technology in the past. In particular, brushless DC motors have not been put into commercial operation until the recent years, as electronic technology has been changing with each passing day. In essence, they still belong to the category of AC motors.
Soon after the brushless motor was invented, people invented the DC brush motor. Since the DC brush motor has a simple structure, is easy to produce and process, is easy to maintain, and is easy to control; the DC motor also has the characteristics of fast response, large starting torque, and the ability to provide rated torque from zero speed to rated speed, it has been widely used since its introduction.
2. Brushed DC motor has fast response speed and large starting torque
The DC brushed motor has a fast starting response speed, large starting torque, smooth speed change, and almost no vibration from zero to maximum speed. It can drive a larger load when starting. The brushless motor has a large starting resistance (inductive reactance), so the power factor is small, the starting torque is relatively small, there is a buzzing sound when starting, accompanied by strong vibration, and the load driven when starting is small.
3. The DC brush motor runs smoothly and has good starting and braking effects
Brushed motors adjust speed by voltage regulation, so starting and braking are smooth, and they are also smooth when running at a constant speed. Brushless motors are usually digital frequency conversion controlled, which first converts AC into DC, and then DC into AC, and controls the speed by changing the frequency. Therefore, brushless DC motors do not run smoothly when starting and braking, and have large vibrations. They are only stable when the speed is constant.
4. High control accuracy of brushed DC motor
Brushed DC motors are usually used with reduction gearboxes and encoders to increase the motor's output power and control accuracy. The control accuracy can reach 0.01 mm, which allows the moving parts to stop almost anywhere you want. All precision machine tools use DC motor control accuracy. Brushless DC motors are not stable during starting and braking, so the moving parts will stop at different positions each time, and must be stopped at the desired position through positioning pins or limiters.
5. DC brush motor has low cost and easy maintenance
Since brushed DC motors have a simple structure, low production cost, many manufacturers, and relatively mature technology, they are widely used, such as in factories, processing machine tools, precision instruments, etc. If the motor fails, you only need to replace the carbon brush, and each carbon brush only costs a few yuan, which is very cheap. Brushless DC motor technology is immature, the price is high, and the application range is limited. It should mainly be used in constant speed equipment, such as variable frequency air conditioners, refrigerators, etc. Brushless DC motors can only be replaced if they are damaged.
6. No brush, low interference
The brushless DC motor has removed the brushes. The most direct change is that there are no sparks generated when the brushed motor is running, which greatly reduces the interference of sparks on remote control radio equipment.
7. Low noise and smooth operation
The brushless DC motor has no brushes, so the friction is greatly reduced during operation, running smoothly and with much lower noise. This advantage is a huge support for the stability of model operation.
8. Long service life and low maintenance cost
Without brushes, the wear of the brushless DC motor is mainly on the bearings. From a mechanical point of view, the brushless DC motor is almost a maintenance-free motor. When necessary, only some dust removal maintenance is required.
Brushless DC Motor Control Principle
Motor drive control is to control the rotation or stop of the motor, as well as the speed of rotation. The motor drive control part is also called electronic speed controller, or ESC for short . ESCs are divided into brushless ESCs and brushless ESCs according to the motors used.
The permanent magnet of a brushed DC motor is fixed, and the coil is wound around the rotor. A brush is intermittently in contact with the commutator to change the direction of the magnetic field to keep the rotor rotating continuously. As the name suggests, a brushless DC motor does not have so-called brushes and commutators. Its rotor is a permanent magnet, and the coil is fixed and directly connected to an external power supply. The question is, how to change the direction of the coil magnetic field? In fact, a brushless DC motor also requires an electronic speed regulator outside. To put it simply, this speed regulator is a motor drive. It changes the direction of the current inside the fixed coil at any time to ensure that the force between it and the permanent magnet is mutually repulsive, so that continuous rotation can continue.
Brushed motors can work without ESCs, and can work by directly supplying electricity to the motor, but the motor speed cannot be controlled in this way. Brushless DC motors must have ESCs to work, otherwise they cannot rotate. The DC power must be converted into three-phase AC power by the brushless ESC and then transmitted to the brushless DC motor for rotation.
The earliest ESCs were not like the current ESCs. They were all brushed ESCs. You may ask, what is a brushed ESC and what is the difference between it and the current brushless ESCs. In fact, the difference is huge. Both brushed and brushless ESCs are based on motors. The rotor of the current motor, that is, the rotating part, is all magnets, and the coil is the stator that does not rotate, because there is no carbon brush in between. This is a brushless DC motor.
As for brushed motors, as the name implies, they have carbon brushes, so they are brushed DC motors. For example, the motors used in the remote control cars that children usually play with for 10 to 20 yuan are brushed DC motors. The ESCs are named after these two types of motors, namely brushed ESCs and brushless ESCs. From a professional point of view, brushed ESCs output direct current, while brushless ESCs output three-phase alternating current. Direct current is the electricity stored in our batteries, which has positive and negative poles. Our household 220V power supply , and the power supply used for mobile phone chargers or computers are all alternating current.
Alternating current has a certain frequency. In layman's terms, it is a line that exchanges positive and negative, positive and negative back and forth; direct current is a line that has positive poles and negative poles. Now that we have figured out alternating current and direct current, what is "three-phase electricity"? Theoretically, three-phase alternating current is a form of electricity transmission, referred to as three-phase electricity. It is a power source composed of three alternating potentials with the same frequency, equal amplitude, and phase difference of 120 degrees. In layman's terms, it is the three-phase alternating current we use at home. Except for the voltage, frequency, and drive angle, everything else is the same. Now you know about three-phase electricity and direct current.
The brushless ESC inputs direct current, which is stabilized by a filter capacitor. Then it is divided into two paths. One path is used by the BEC of the ESC . The BEC is used to power the receiver and the ESC's own microcontroller. The power line output to the receiver is the red and black lines on the signal line. The other path is used by the MOS tube. Here, when the ESC is powered on, the microcontroller starts to start, driving the MOS tube to vibrate, making the motor emit a dripping sound.
After starting, it will be ready for operation. Some ESCs have a throttle calibration function. Before entering the standby mode, it will monitor whether the throttle position is high, low or in the middle. If it is high, it will enter the ESC stroke calibration. If it is in the middle, it will start to send out an alarm signal and the motor will beep. If it is low, it will enter the normal working state. After everything is ready, the MCU in the ESC will determine the output voltage and frequency according to the signal on the PWM signal line, as well as the driving direction and timing angle to drive the motor speed and direction. This is the principle of brushless ESC. When the motor is driven, there are 3 groups of MOS tubes working in the ESC, each with 2 poles, one to control the positive output and the other to control the negative output. When the positive outputs, the negative output does not, and when the negative outputs, the positive output does not, so that AC is formed. Similarly, all three groups work in this way, and their frequency is 8000HZ . Speaking of this, brushless ESC is equivalent to a frequency converter or speed regulator used on motors in a factory.
The input of the ESC is DC, usually powered by a lithium battery. The output is three-phase AC, which can directly drive the motor. In addition, the model aircraft brushless electronic speed controller has three signal input lines, which input PWM signals to control the speed of the motor. For model aircraft, especially quadcopters, due to their particularity, special model aircraft ESCs are required.
So why do quadcopters need special ESCs? What's so special about them? A quadcopter has four propellers, which are arranged in a cross structure. The propellers can be rotated in forward and reverse directions, which can offset the spin problem caused by the rotation of a single propeller. The diameter of each propeller is very small, and the centrifugal force of the four propellers is dispersed when they rotate. Unlike the propellers of a helicopter, only one can generate concentrated centrifugal force to form a gyroscopic inertial centrifugal force, which keeps the fuselage from tipping over quickly. Therefore, the update frequency of the servo control signal commonly used is very low.
In order for the quadcopter to react quickly to cope with the drift caused by attitude changes, a high-response speed ESC is required. The update speed of conventional PPM ESC is only about 50Hz , which cannot meet the speed required for this control. In addition, the PPM ESC MCU has built-in PID speed control, which can provide smooth speed change characteristics for conventional aircraft models, but it is not suitable for quadcopters, which need fast-response motor speed changes. Using a high-speed dedicated ESC and the IIC bus interface to transmit control signals can achieve hundreds or thousands of motor speed changes per second, so that the attitude can be kept stable at all times during quadcopter flight. Even if it is suddenly impacted by external forces, it is still safe and sound.
If you are looking for a professional screwdriver manufacturerto customize your precision screwdriver set, feel free to contact us today! We provide high-quality, customizable toolsfor various repair needs.