How to Remove a Damaged Screw or Bolt With a Screw Extractor
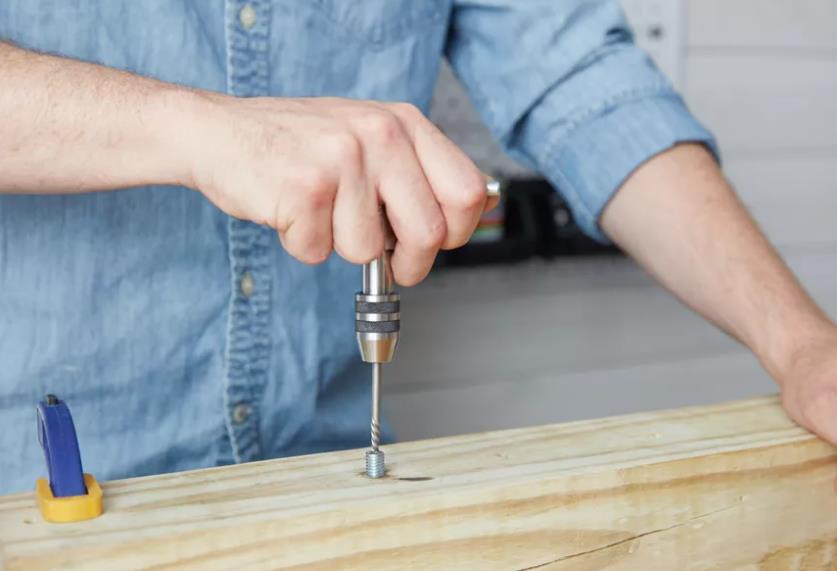
Removing a screw or bolt can be exasperating if the slots on the screw or the head of the bolt have been damaged from efforts to remove the fastener. This can easily happen if the fastener is rusted in place, or if you've used the wrong-sized tool. A few slips of the screwdriver or wrench and the head of the screw or bolt can be so damaged that it's almost impossible to get a good grip on it.
To your rescue comes this clever little accessory—the screw extractor. Screw extractors come in a range of sizes for screws of diameters ranging from 3/32 inch to upwards of 1/2 inch. They can be used on all manner of screws, as well as many bolts.
Screw Extractor Design
A screw extractoris a high-strength steel shaft with a square head on one end and reverse tapered cutting screw threads on the other end. The square head fits into a T-handle that's used to turn the extractor. You can also grip and turn the head of the tool with locking pliers.
The tapered threads are at the business end of the tool. These are designed to screw backward (counterclockwise) into the head of the screw or bolt after a pilot hole has first been drilled. The end is sharply tapered so that the extractor digs into the damaged screw deeper and tighter as the extractor is turned. So while you're turning the extractor counterclockwise, it's digging into the damaged screw more and more as the damaged screw is backing out.
A T-handleis a useful accessory when using a screw extractor. Named for its shape, the handle fits over the end of an extractor bit. T-handles are made to fit a variety of extractor sizes, and many types also work with taps for threading holes. If you don't have a T-handle, you can turn a screw extractor with locking pliers.
Tip
It's important that you use the proper size extractor. Too large and it will not leave enough metal to properly hold the extractor, and it will damage the threads holding the screw or bolt. Too small and the torque required for larger screws and bolts may cause the extractor to break. This chartcan help you determine the correct size to use.
How to Use a Screw Extractor
Drill a Pilot Hole
To use a screw extractor to remove a screw, drill a pilot hole into the center of the damaged screw, using a power drill and a twist bit of appropriate size. If the head of the damaged screw is rough or uneven, it can help to start with a very small pilot hole, such as with a 1/16-inch bit. Make sure to place a drop or two of motor or cutting oil on the damaged screw before drilling; it will help keep the drill bit from overheating.
Then drill a larger hole with the bit sized for the extractor. The pilot hole diameter varies according to the extractor size you are using. Follow the recommendations on the package that came with the extractor.
Tip
Since you're drilling into metal, keep the drill speed slow and steady; drilling too fast will overheat the bit and dull it quickly. Be very careful not to break off the drill bit inside the hole, especially when drilling with small bits.
Extract the Screw
Attach the extractor bit firmly to a T-handle or grip it with locking pliers. Place the extractor bit into the pilot hole in the damaged screw.
Using a hammer, tap the extractor firmly into the pilot hole. Apply downward pressure on the extractor while turning it counterclockwise to remove the damaged screw.
If the extractor slips and loses its bite in the screw, try tapping the extractor again to get a better seat in the pilot hole. Push down more firmly as you turn the extractor counterclockwise. If that doesn't work, enlarge the pilot hole just slightly and try again.
If you are looking for a professional screwdriver manufacturerto customize your precision screwdriver set, feel free to contact us today! We provide high-quality, customizable toolsfor various repair needs.